Can you give us some background on the company and an overview of the products and services it provides to the pharmaceutical industry?
Operating through six production sites, IMA Life (Aseptic Processing & Freeze Drying Solutions) is one of the three pharmaceutical divisions of the IMA Group, world leader in the design and manufacture of automatic machines, highly specialized in the production of complete aseptic lines from the initial washing of the bottles, through depyrogenation, filling, capping, decontamination, up to and including secondary packaging. All this with or without freeze-drying systems and, in the part where the product is exposed, using an isolator or other containment solutions.
IMA LIFE aseptic filling lines are intended for applications requiring equipment incorporating topmost scientific and technological content, where the industry is obliged to respect very strict standards (GMP – Good Manufacturing Practice). Line performance is from 400 up to 600 units per minute, satisfying the most demanding requirements coming from the aseptic, biopharmaceutical and pharmaceutical markets. Each solution represents consolidated technology, acquired not only through experience spanning over 60 years, but also thanks to ongoing partnerships and large-scale projects developed and managed with leading pharmaceutical companies worldwide.
At IMA Life North America Inc., the IMA Life production facility based in Tonawanda (NY), US, we are involved in the pharmaceutical lyophilization market by offering equipment manufacturing & services, novel technology development and providing process, scale-up and tech transfer support. The Tonawanda, NY facility is specialized in the production of a wide range of custom-built industrial & scale-up freeze drying equipment (including also solutions for pilot work, clinical trial production or even R&D lab. FD) with installations in over 50 different countries and has pioneered the development of several technologies aimed at improving the freeze-drying equipment and process. A truly global Service Team ensures an active network assisting Customers far beyond natural borders and cultural barriers.
What are some general industry issues pharmaceutical companies are facing regarding manufacturing and specifically the management of equipment maintenance and downtime?
Manufacturing in the aseptic pharmaceutical industry is primarily driven by production campaigns, with each campaign setting a batch target. Efficiency and scheduling of resources becomes critical to achieving this throughput. Equipment maintenance is a critical component to ensure optimal product quality and process performance. However, due to some common practices followed today, there are many challenges in maintenance and management of equipment and processes.
Subscribe to our e-Newsletters
Stay up to date with the latest news, articles, and events. Plus, get special offers
from American Pharmaceutical Review – all delivered right to your inbox! Sign up now!
One such practice is routinely scheduled preventive maintenance, which is common in the pharmaceutical industry. However, a major drawback of a time driven approach is that many equipment is either over or under maintained. Not only does preventive maintenance have a significant cost, it also doesn’t account for changes in equipment performance over time.
Similarly, unplanned downtime caused due to equipment failures and a reactionary approach to such failures is another situation that’s undesirable. Failures in equipment in some cases may be sudden, but creep failure is a much more likely scenario that can eventually culminate in process deviations leading to a batch loss. For example, a gradually increasing vacuum pulldown time may indicate system leaks or a pump that isn’t performing as expected. Unless such outputs are derived and monitored, an equipment failure may occur and stop production campaigns.
What is Continuous Process Verification and how have worldwide regulatory agencies provided guidance to pharma companies to maintain the assured state of a validated system.
The U.S Food and Drug Administration (USFDA) as well as the European Union’s EMA have issued regulatory guidance regarding Continued Process Verification (CPV). The objective behind CPV is to ensure that a process remains in its validated state throughout the commercial manufacturing process. This includes a system for detecting any unplanned departures from the designed process. It recommends the establishment of an ongoing program to collect, analyze and process data that may relate to product quality. Any deviations from a process or product quality must be evaluated and the root cause of such deviations need to be reported.
In a freeze-drying process, each component such as compressors or vacuum pumps has a direct impact on a drug product’s critical quality attributes (CQAs). Process parameters such as shelf temperature and chamber pressure have a similar relationship to product quality. The design and operation of the IMA Life’s Data Analytics platform is based on such regulatory guidance.
Looking specifically at the freeze-drying process, how can companies use data analytics to reduce costs associated with maintenance and downtime?
During a freeze-drying cycle, there is tremendous amounts of process and equipment data that is collected. In a typical production dryer averaging 200 signal tags, there are over 5 billion data points logged in a year. Some of the current root cause approaches are performed using a multi variate data analysis methods which uses historical data from different sensors. Building on the capabilities of MVDA, data analytics models can enable real time data monitoring and event prediction.
Let’s consider a production freeze dryer which has a refrigeration system known for temperature fluctuations. A model to alert the user prior to excursions in condenser temperature or pressure fluctuations was developed. During this analysis, we found that increases in condenser temperature follow an oscillating pattern which was then captured. By training this model and performing validation on large amounts of data, lead times to failure spanning from 2-10 hours were observed.
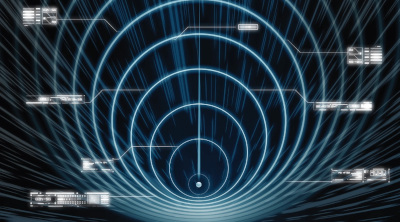
In addition to process metrics, freeze dryer equipment subsystems were modeled as well. A typical vacuum pump assembly designed for a freeze dryer can evacuate the system in 30-40 minutes. However, during historical analysis of a freeze-dryer, an increasing vacuum pulldown time trend was observed, and it was reported that a vacuum pump eventually failed. There were 15 cycles between the first evacuation time outlier and observed pump failure. Had this phenomenon been tracked with system alerts, service teams may have been able to respond proactively to minimize equipment downtime.
By deploying such specific analytics, pharmaceutical companies can leverage equipment and process knowledge to increase overall equipment effectiveness (OEE).
Can you tell us about some specific data analytics tools your company has developed to assist companies with their freeze-drying efforts? What benefits have companies seen by implementing these technologies? Can you provide some examples?
IMA Life’s Data Analytics platform – the Sentinel-Lyo is built surrounding an overall health management principle, where process and equipment knowledge can be combined to provide system performance outputs to the user. This platform follows a three-step approach where - a network of sensors installed across the freeze dryer monitor system condition, several equipment and process specific models analyze incoming sensor data, and predictive analytics output alerts and novel patterns intended for failure prevention. Similar to some examples of analytics mentioned earlier, a number of data and predictive model analytics have been developed as a part of this platform.
The benefits can be seen from both an equipment and process perspective. Each output from the analytic models may be seen as enabling informed manufacturing. Some of the overall benefits that a company sees include a possible reduction in downtime, improved equipment status awareness, better tools for historical data analysis, failure and process deviation prediction capabilities, as well as compliance with regulatory guidance through process diagnostics.
Looking ahead, what are the company’s goals regarding its products and technologies to aid pharma companies with their data analytics capabilities to reduce costs and improve the quality of their products?
To determine next steps, we must try to image what aseptic manufacturing of the future might look like. Imagine a control room with equipment and process experts analyzing the overall system health and providing valuable feedback to manufacturing stakeholders. This intelligent feedback enabling an end-to-end streamlined service, is what IMA’s goal is regarding the Sentinel-Lyo technology.
Implementation of data and predictive analytics for monitoring of aseptic pharmaceutical manufacturing equipment is one of the first, yet key components in IMA Life’s overall digital technologies adoption. These digital transformation efforts are being driven, in part due to improved system health monitoring and failure predictions, but also through increased interest from IMA’s pharmaceutical customers. After successful development of a data analytics product for freeze dryers, IMA Life has engaged in similar development efforts on related aseptic equipment such as isolators.
Keeping in mind an ambitious goal of autonomous or prescriptive freeze drying, a stepwise approach needs to be adopted to keep capturing process and equipment knowledge into different models. This will enable moving away from a manual reaction-based approach that is commonly seen in the industry today. At IMA, we have implemented, what we believe to be next steps in this ladder towards autonomous freeze drying.
By deploying this product, we aim to demonstrate the capabilities of data and predictive analytics in a manufacturing environment. At the same time, this platform ties into IMA Life’s service organization where a team of subject matter experts can provide immediate insights into process or equipment system health.