Kaitlyn Vap - Life Sciences Lead Product Application Specialist, SUEZ Water Technologies
Implementing Real-Time Testing (RTT) or Real-Time Release Testing (RTRT) in pharmaceutical manufacturing is becoming a more widespread goal to improve efficiency when it comes to assuring quality attributes of raw materials, such as water for pharmaceutical production. As part of a successful RTT program, it is critical to consider the approach to data integrity, data transfer, and data security. Including these elements in the RTT strategy and implementation plan enables manufacturers to better align with today’s data integrity requirements and get the most out of their RTT program.
21 CFR Part 11 and ALCOA+
Data transfer and data integrity have been long standing principles upheld by the Food and Drug Administration’s (FDA) 21 CFR Part 11 guidance and ALCOA+ principles respectively. 21 CFR Part 11 was released in 1997 in response to the digital age with the intention of maintaining data security through the electronic transfer of data. 21 CFR Part 11 enforces controls and requirements related to the following:
- Data security
- Data retrieval
- Validation
- Audit trails
- Operational, authority, and device controls
- Electronic signatures
ALCOA was originally introduced in the 1990s by the FDA with the ALCOA+ revision and addition taking form in 2010. ALCOA set the guiding principles for data integrity in a certified good manufacturing practice (cGMP) environment. The ALCOA+ principles can be seen below:
- Attributable – data must be traceable
- Legible – data must be understandable
- Contemporaneous – data must be recorded as the measuring process is taking place
- Original – data must be in an unaltered state
- Accurate – data must be truthful
- Complete – data should be all encompassing
- Consistent – data must be recorded in a defined manner
- Enduring – data must be maintained and stored through a retention period
- Available – data must be accessible
With the adoption of electronic records in the digital age, 21 CFR Part 11 and ALCOA+ provide guidelines for maintaining data integrity, a concept which “refers to the completeness, consistency, and accuracy of data” according to the FDA’s Data Integrity and Compliance with cGMP Guidance for Industry document.
Data Transfer Pathway
Equipment and instrumentation, with the ability to output data in any department within a pharmaceutical site, typically transfers data in a tiered manner shown in Figure 1. Data generation from equipment and instrumentation in use is transferred to data processors such as a programmable logic controller (PLC) or proportional integral derivative controller (PID). At these controllers, data is continuously monitored and trended for process control purposes. From the control level, data is transferred to a supervisory control and data acquisition (SCADA) system or historian. This supervisory level compiles data and functions as a control, alarm, and distribution center. Data is then transferred to a manufacturing execution system (MES) with the ability to track raw materials and finished product. The intent of an MES is to use the output data across multiple platforms to improve process efficiencies through optimizing the production cycle. The final tier data is transferred to is an enterprise resource planning (ERP) system. The function of an ERP is to optimize business efficiencies by monitoring scheduling, inventory, and order processing.
As data transfer applies to laboratory and production environments responsible for testing quality attributes of raw materials and final product, data must be compiled into a report for specific individuals to sign off on the compliance of a measurement reflective of a quality attribute. These reports are entered into an electronic batch record (EBR) for data storage purposes.
Data Handling and Reporting in Accordance with ASTM E2656
Data integrity, data transfer, and data security all apply to real-time testing (RTT) and real-time release testing (RTRT) of water for pharmaceutical production. In the migration from laboratory-based water release to online/automated water release, the way in which data is transferred in Figure 1 remains the same; however, the amount of data that is captured may vary. Laboratory-based water quality evaluation requires a single data point for a USP <643> limit test, but when evaluating the water quality using an online instrument, data points are generated on a more frequent and, in some cases, continuous basis. Since this generates a high volume of data, ASTM E2656 – Standard Practice for Real-time Release Testing of Pharmaceutical Water for the Total Organic Carbon Attribute – recommends creating and validating a report generation system.
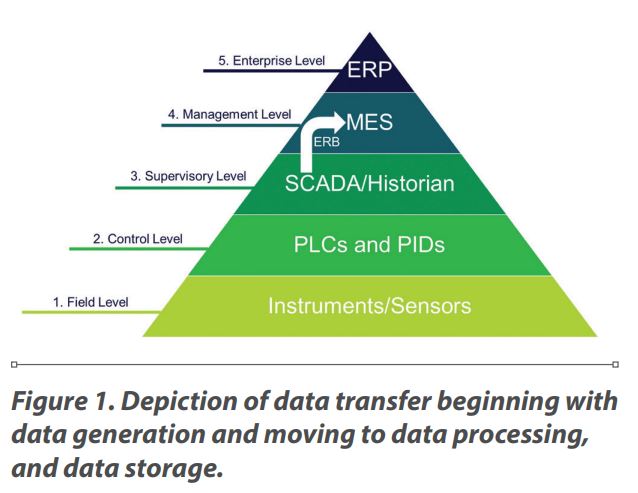
A report for RTT data should start with a defined collection period. The collection period should align with the production schedule to ensure the data isolated from the online instrument of record is indicative of the timeframe in which water entered a new production run. With a defined collection period, the remainder of the report might include the maximum, minimum, and average of the collection period, and any notable alert and action events.
When considering the frequency of measurements, ASTM E2656 recommends considering the instrument delay time, response time, cycle time, update rate, rate of change of Total Organic Carbon (TOC) concentrations, rate of water consumption, detection, probability of exceeding TOC specification levels, and comparative costs of Out-Of-Specification (OOS) product. The purpose of assessing these variables is to build confidence in the ability of the instrument to detect and measure TOC concentration variations.
The value of transitioning to RTT is that it provides the ability to monitor and control the process while also releasing water for TOC and conductivity. Because online instrumentation offers higher volumes of data for monitoring and control purposes, ASTM E2656 acknowledges that for release purposes “any chosen frequency will be better than the off-line sample testing that can only provide a snapshot in time.”
Software Solutions – DataShare Elite
When transitioning to real-time testing, the origin of the data shifts from a quality laboratory environment to a production environment; therefore, it is helpful to have software to centralize data. DataShare Elite is a Sievers software solution developed for automating the transfer and retrieval of data pertaining to quality attributes. DataShare Elite software provides a single, central location to manage all Sievers TOC and conductivity data – pulling from multiple instruments in various environments. This allows quality departments to easily access real-time data, generated in a production environment, and remotely sign-off on measurement compliance for raw materials (water) to enter production.
DataShare Elite provides a highly customizable enterprise solution with ALCOA+ data integrity compliance features, 21 CFR Part 11 compliance, and influence on cGMP guidelines using new data transfer, data management, and data security features seen below:
- Data Transfer
- Remotely connect or import data over a secure network
- Data Security
- Customizable password protection
- Unique User ID requirements
- Data encryption
- Electronic signatures
- Easy import and review of audit trails
- Customizable access, roles, and permission
- Network-based Data Management
- Closed system architecture
- Compatible with Active Directory (AD)
- Use with local server or an existing enterprise Microsoft SQL server
- Customizable data transfer and exporT
- Remote Data Management
- Review instrument data remotely and electronically sign-off on
- Calibrations
- Verifications & system suitability tests
- Validations
- TOC sample results
- Audit trail
- Easily search, filter, parse out data and save protocol results
- Manage and transfer data from the production environment and back for faster release of water systems
- Manage real-time data and audit trails as events happen
- Data Visualization
- Qualitative and quantitative data
- Graphing and export capability
- Secure Data Integration
- Easy to integrate into LIMS and MES systems
These functions lend themselves to ASTM E2656 guidance practices on report generation and measurement frequency for real-time testing. Having the ability to review and trend real-time data simplifies processes and allows release testing to happen much faster through secure, encrypted data transfer. Digitally signing records with accurate and customizable signatures offers a more efficient record review process. Ultimately, these qualities align with the value of transitioning to real-time testing – to optimize efficiencies and enhance patient safety – while providing a simple solution to maintaining data integrity and 21 CFR Part 11 compliance.
Kaitlyn Vap is the Life Sciences Lead Product Application Specialist responsible for supporting Sievers total organic carbon (TOC) customers. She works with companies in the pharmaceutical industry to implement Sievers analytical instruments for the validation of laboratory water and drug products in accordance with global pharmacopeia regulatory standards. As an application specialist, she also explores new and/or developing applications to streamline the process of water and drug product testing. Kaitlyn holds a B.S. in Chemical Engineering from the University of Wyoming.
Subscribe to our e-Newsletters
Stay up to date with the latest news, articles, and events. Plus, get special
offers from American Pharmaceutical Review delivered to your inbox!
Sign up now!