Pamela Raymond,1 Sarah Ray, 2 Lauren Sanmartin,3 and Donald Singer,4 - 1,2GSK, 3Gilead Sciences, 4Ecolab Life Sciences
Abstract
We often take for granted the human aspect of meeting objectives for compliance. While the patient is our ultimate customer, developing a program of contamination control is complex and is significantly dependent on proper human behavior to achieve successful outcomes. The interdependencies of a robust process, quality of input materials, controlled facility and equipment, and operators following validated procedures are the parts of a puzzle that must fit well to ensure successful implementation of a contamination control strategy.
Designing a sterile product process can, and does, move in the direction of removing human operators wherever possible. Robotics and containment provide methods to reduce human intervention. Yet, pharmaceutical cleanrooms commonly do not operate without human presence, although with varying degrees of activity. One of the routine human activities that support contamination control of a cleanroom is cleaning and disinfection. There are equipment and tools that can be sterilized prior to manufacturing use, but there are also many surfaces and areas that require routine oversight and disinfection to maintain control over microbiological cross-contamination.
This article will discuss the best practice approach for supervising and training cleanroom cleaning operators and managing the cleaning activities.
Introduction
The human aspect of meeting objectives for compliance is often taken for granted. While the patient is our ultimate customer, developing a program of contamination control is complex and significantly dependent on the correct human behavior to achieve successful outcomes. The interdependencies of a robust process, quality of input materials, controlled facility and equipment, and operators following validated procedures are each a piece of a puzzle that must fit well to ensure successful implementation of a contamination control strategy (Figure 1).
Designing a sterile product process can, and does, aim to remove human operators wherever possible. Robotics and containment provide means to reduce human intervention. Yet, pharmaceutical cleanrooms commonly do not operate without human presence, although with varying degrees of activity. One of the routine human activities that support contamination control of a cleanroom is cleaning and disinfection. There are equipment and tools that can be sterilized prior to manufacturing use, but there are also many surfaces and areas that require routine oversight and disinfection to maintain control over microbiological contamination.
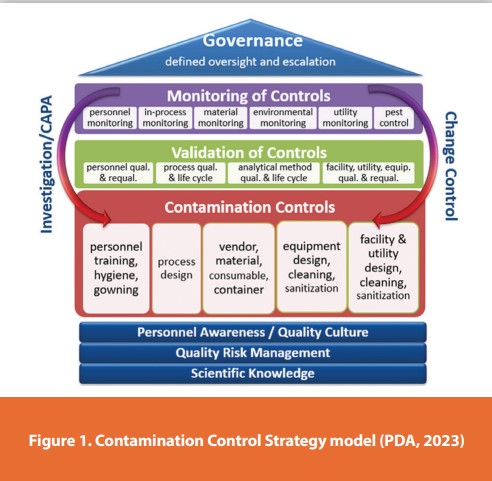
The cleaning and disinfection activities are performed by individuals who may have this activity as a single, focused role or as one in a list of many other roles. There can be one or more individuals assigned to perform this role. The individuals assigned to cleaning and disinfection can be either full-time or part-time employees of the cleanroom owner, or they could be third-party contractors responsible for one or more cleanroom facilities. Regardless of the employer, the individual(s) who performs cleaning and disinfection should be given sufficient training, adequate tools, respect by their supervision, and they should show good behavior and integrity for the purpose and facility in which they work. A consistent and successful cleanroom cleaning staff is aware of the purpose and importance of their responsibilities. Their management should have high quality oversight.
This article will discuss the best practice approach and tips for supervising and training cleanroom cleaning operators and managing the cleaning activities.
Training
Learning foundation
A cleanroom cleaning operations team can consist of a range of demographics, cultures and personalities, with diversity just as significant as in the foundations of a pharmaceutical workplace.
Many ‘GMP cleaners’ (GMP: good manufacturing practices) start their careers as non-GMP cleaners (such as with office and general facility cleaning), giving them a foundation with which they can build and can learn about GMP manufacturing and the cleanroom contamination controls, including cleaning and disinfection. Training to develop the cleaner’s contamination control thinking as well as reinforce best practices for cleaning and disinfection will require some time investment. Training should be given in appropriately timed sessions and should cover the basics of sterile manufacturing, sterility assurance, microbiology, safe handling of cleaning and disinfection agents, preparation and disposal of disinfectants, and appropriate application methods.2 Training is considered an initial introduction of ideas and concepts, whereas learning is an ongoing investment in the expansion and retention of information. When planning weekly or monthly staff team meetings, it is a good practice to establish time in the agenda for learning.
Provide a format for the training content, based on the communication style(s) of the team (know your audience). If you have more junior members of the team looking for development opportunities, perhaps look to engage them to create and deliver the training packages. Not only will this expand the cleaning team’s understanding of your operation and the importance of their role in it, but it will also help to foster wider team engagement and community.
The foundation of a good cleaning team is providing and instilling a sense of ownership and accountability. The most important aspect is how their work impacts the process.
Along with the role ownership objective, they should be trained on the manufacturing operation of a cleanroom and how critical cleanroom operations are. The use of real-life examples and simplicity is helpful. For example, relate the cleanroom activities to the resulting end product which is critical and potentially dangerous to the patient. With this perspective, the cleaning team can understand the significance of their activities. In other words, control and patient safety starts with how the cleanroom is controlled and maintained, including their cleaning actions in the cleanroom. The flipside of this could also be useful for learning: if you don’t have a clean facility to work in, you don’t have a place to manufacture medicine, and all involved in a manufacturing process are ‘cogs in the wheel.’ If one of those cogs break down, then we don’t have an aseptic operation. Everyone has an equally important role to perform.
The training needs to ensure that at the end the cleaning operators are as independent as possible, because they’re on their own. They need to be able to make appropriate decisions, follow procedures and know how that is going to impact the processes down the line from their cleaning. So, the real key training for the cleaning operators is how their work fits into the quality of the process.
Another good trait of a cleaning operator is knowing when to ask for help, being able to speak up and let someone know potential issues. A sense of ownership should be instilled during the training so that the cleaning operator feels empowered to speak up and communicate. This is important for a cleanroom environment. That’s the way to mitigate. You mitigate early and you mitigate as soon as you know. With a team, it needs to be collaborative.
Key Knowledge and Skills
These are some of the key areas of knowledge and skills to express in a holistic training program:
- Aseptic gowning and gloving procedures
- Microbiology
- Cleanroom controls
- Decontamination agent applications
- Safe handling and storage of cleaning agents and equipment
The cleaning team should understand what the cleanroom is and the ancillary rooms that they will be entering and cleaning, and at a high level, the manufacturing function performed in each of these rooms.
A high-level explanation should include the engineering controls, (e.g., HEPA filters, air pressure and air flow), that are built in place which support the cleanroom such as equipment, instrumentation and design aspects for maintaining control for high quality air and contamination prevention.
It is good to mainly focus on the people aspects, as humans are the most common source of contamination in a cleanroom. Subsequently, what do we do about that? This is where training objectives get into the gowning behaviors and why it’s so important for the cleaning operators to understand and be skilled in proper aseptic gowning and cleanroom behaviors, just as the aseptic operators are expected.
Aseptic Gloving
Gloving training should develop a person’s understanding and experience with microorganisms. Start with proper sterile gloving procedures, and fundamentally show individuals where and how microorganisms can be transferred.
For example, some trainers use a plating exercise using the steps below:
1. Each operator’s (and trainer’s) fingers and wrists are sampled microbiologically using plated media, prior to putting on gloves or sanitizing hands.
2. They are then instructed to put on the sterile gloves ‘like any other glove’ (e.g., garden glove) they have donned before.
3. Another microbiological sampling of the operator’s gloves is then performed.
4. The trainer then puts on their own sterile gloves in an aseptic manner, explaining how and why this procedure is followed, and then has them sampled.
The explanation is a good transition into aseptic glove training. After a couple of days of plate incubation, the team is brought together to see the microbiological results of non-sanitized hands, poor glove handling, compared to the lower bioburden results from proper aseptic glove handling.
The glove training will also stress the importance of skilled aseptic technique and the consequences of good and poor technique, which also leads to what surfaces a cleaning operator should and should not contact with their gloved hands in the cleanroom they are cleaning.
In simple terms, a sterile or decontaminated surface can remain as such until it has been contacted by a non-sterile entity, such as human gloved hands. Every operator should be aware of what they touch in a cleanroom. Some people have personalities that enhance clean surface awareness, and some do not. It is important for a trainer to influence improved clean surface awareness in initial and ongoing training.
Aseptic Gown Training and Qualification
Gowning training and qualification of cleaning personnel should align with aseptic operator training and qualification. Each individual should understand how to follow the procedure and a trainer should be able to express improvement recommendations at any time. Both a technical assessment and a microbiological assessment should be complementary for qualification and each requalification. Increased frequency of technical assessments (how to gown properly) may provide for development of a timelier improvement plan before problems lead to contamination issues. The use of in-operation cameras could complement or replace periodic technical in-person assessment.
For camera use, they should not be used in training to show bad examples. They should only be used for investigations or in training to show good examples, which is a better culture to instill. However sometimes it is helpful to watch yourself, as it can be used for improvements in training for proper aseptic gowning.
The capabilities and experience of a good trainer are critical for this training. Knowing individual’s patterns during gowning exercises are important and the ability to constructively express improvement recommendations will enhance the integrity of the individuals for cleanroom cleaning activities.
Cleaning and Disinfection in the Cleanroom
The application of agents onto surfaces by cleanroom cleaners is critical. Just think about the cleanroom space that has all white walls. The design of a cleanroom looks like one continuous space. There are no markers when you’re looking at the walls to clean, so an amount of patience and focus is needed during a cleaning. To make sure agents are applied in overlapping strokes, it can be a challenge when the application is barely visible on the surface. The cleaners need to have ironclad focus.
Successful cleaning and disinfection comes from consistency and thoroughness. Practical-based training should be step-by-step and include an explanation of the ‘why’ behind the defined procedure. People are naturally curious, and whether they fully understand it or not, a trainer should give them the opportunity and chance to show that they understand the method(s). As in any training, encourage and accept all questions that people ask. The objective of this training is to embed that sense of ownership and create a ‘speak-up’ culture.
Cleanroom cleaners may have the hardest job to perform in a cleanroom. It’s physically hard, and quite regularly these activities are performed on their own. A typical ‘buddy system’ within the cleanroom, which is to watch and provide feedback such as saying, “Hey, you’ve got exposed skin” or “Don’t touch that bag on the shelf”, is missing. Realizing this independent, yet critical lack of oversight, leads to the understanding of how important communication is between the cleaning team and the aseptic operations team. Environmental monitoring is not perfect and cannot detect all possible contamination points, so operations must rely on (cleanroom cleaning) people’s integrity and honesty.
Where possible and appropriate, some firms have cleanroom cameras to monitor aseptic operations, including process simulations and off shift activities. If present and operating, the cameras can be used for contamination investigations. Encouraging the speak-up culture and documentation of atypical situations is a way to reduce fear of the use of cameras by encouraging people to share potential deviations in procedures without negative personal consequences.
Selection of Cleaning Tools
The cleaning team and their supervisor should participate in any decision-making related to identifying the correct tools to use, and in some cases the disinfectant agents. Meeting with a supplier can accomplish this. The cleaning team should be able to handle the tools for weight and ergonomic feel for actual application use. This would be followed by practicing use of the tools with an experienced application trainer.
Application of Cleaning and Disinfection Agents
Training should include an explanation of the importance of the cleaning step prior to disinfection. An explanation of the significance of cleaning of soil and/or residue prior to effective disinfection practices is valuable.
Cleaning is a physically demanding job, so part of that technique is knowing when you’ve reached either your mental or your physical capacity and being able to have enough robust staff that you can alternate people. That kind of understanding and open communication culture within the cleaning team would be vital. It can be beneficial to include breaks in a cleaning schedule; because if you don’t pay attention to the GMP cleaners’ emotional and physical state, then it’s very possible to reduce the quality of the process.
Key soft skills are: the focus and the attention to detail. The repetition, being able to overcome that repetition and not drift is really difficult for cleanroom operators and the cleaners.
Discuss and/or create ways to help cleaners overcome that in your training program. One consideration is to give them tools, such as checklists that they could follow where they can evaluate their progress.
Build into the process a schedule where they can take a break. Ensure that you give the cleaning team enough time to complete the job without having to rush.
The technique for cleanroom cleaning is not hard when learned. Yet, it must be done and it must be done correctly. It’s more important to focus on how they can maintain that technique once they’ve learned it and over such a large amount of time that it takes to accomplish the cleaning activity.
Training of the application of cleaning and disinfection agents can be shown by standing and starting in the furthest part of the room. The latter approach is common for a facility that is undergoing a regular cleaning and disinfection program. This could be different if, for example, after a shutdown when many people and materials have been moved through the external adjacent areas (e.g., hallways), the soil can be much higher than usual. In this case, cleaners may be asked to ‘clean’ their way into the aseptic core areas, and then subsequently follow the common practice of cleaning from the innermost to the outer areas. Also, express the rationale to the cleaning team for applying disinfection agents from high areas to low areas and then also backing your way out from the furthest point area to the exit, to show that correct procedure is not walking through what has been disinfected and preventing personal bioburden shedding over a place that was just cleaned. So, there is an order of procedural events intended for the way in which an area is cleaned.
One approach to practical-based training that has a history of success is a three-step process:
1. The cleanroom cleaner observes an experienced cleaner once, and then
2. the new cleaner performs cleaning under supervision, then when determined by supervision that they are ready,
3. the cleaner performs independently with an associate watching them without assisting, and then they can get documented approval.
The training needs to be continuous and regularly reinforced. It also can check and make sure that the trainees are up to date with everything that happens on a day-to-day basis and in operations. This is where a quality ‘huddle’ can come in handy on a daily or shift basis.
Contact Time and Surface Compatibility
Training cleaners about surface contact time should include the challenges, e.g., high velocity air movement that dries surfaces more rapidly, surface deviations that make access to contaminants more difficult, differences in surface tension that effect surface coverage, and different surface types that lead to disinfectant efficacy differences. A discussion about different methods of application (wipe, mop, spray and wipe, mechanical action, automated vaporization) can increase the confidence of the cleaners in the selected methods. It should also be highlighted that floors should not be walked on until the whole contact time has been achieved to allow the agent to be effective.
Also helpful is an explanation and discussion about the conditional use of sporicide compared to a regular disinfectant. Simple examples can be used. For instance, when something like a piece of equipment that goes outside of the facility, to get calibrated, and then is brought back into the cleanroom, explain that the common approach is to apply heavy wiping with a sporicide for increasing assurance of the removal of microbial contaminants. Another example could be to explain that sporicide should be used in an appropriate rotation to maintain control over fungi and bacterial spores.
Observing and Evaluating Cleaning Practices
Observing cleanroom cleaning can be a value-added activity for an aseptic operations supervisor. It’s important to not only oversee a cleaning team but to watch how they perform the proceduralized activities, especially if the activities are performed on an off-shift. This can have great impact, because observing the cleaning team activity offers better insight, rather than just depending on what is documented in a cleaning activity logbook. Remember that people are only as good as the training and the communication that’s been provided to them. That will have impact on what or how they are cleaning. Even in a multiple shift cleanroom operation, it is possible to not have sufficient oversight of the cleaning activity and this should be corrected.
Although this evaluation is a type of ‘audit’, it is important not to make the activity audit-like. It is better to explain to the cleanroom cleaners and their supervisor that normal cleaning practices should be evaluated periodically to help them do their jobs more consistently, efficiently and to seek improvement ideas from them. It is not a good idea to place them in a position where they feel they are being scrutinized and that their jobs are at stake. There are many benefits to good management of a cleaning evaluation, some of which include trust, integrity and developing a good quality relationship with those performing the cleanroom cleaning. The thinking should be, “We’re all working towards the best quality process and when you are a part of it and I’m a part of it and we work together, then we’ll make a better process”.
Use of Environmental Monitoring (EM) Data for Cleaning Evaluation
EM data is used by the Quality Control/Quality Assurance group, within a production facility, to support many activities including cleaning. Yet, is there any sharing or communicating of that type of data with the cleaners?
The response and approach should be ‘Yes’. It is important to recognize that if EM samples are taken immediately (and taken correctly) after cleaning there is direct relevance to the cleaning effectiveness. But, be aware and careful that if samples are not taken immediately, and any activity that occurs in the cleanroom(s) before EM samples are taken, this can reduce the direct relevance to cleaning and compound root cause identification.
An initial explanation to the cleaning team on how to understand EM data would be very useful. Microbial recovery can be a potential indication of a much bigger problem. The bigger picture, though, which could be the absence of recovered colonies after cleaning a larger surface area, is that it represents one small sample area. Also, a cleaning operator should not think automatically that a microbial recovery means that any one location needs to be cleaned better. There is a more holistic picture they should understand. A microbiologist can be very helpful in discussing and explaining what thinking and actions can be taken based on EM results and trends.
Training and Communication
Verbal communication is important, but documentation is also important because sometimes you’re not going to be able to reach the people that you need to reach in a timely manner. Good Manufacturing Practices (GMP) is all about documenting at the time of the activity and if something goes wrong, it’s better to document it immediately and then either justify it later or mitigate it later. But if we don’t document, for example, the time or the aspect of what happened, we may lose that information. That’s an important part of the job and a key skill set for someone who’s working off-shift in a GMP process (such as a cleaning and disinfection activity) that has such a real impact on quality of your clean space.
For verbal communication, sometimes language barriers can be hard. If you have a cleanroom cleaning team that has multiple native languages it can be a challenge when training. Having someone that is bilingual within the team would be amazingly helpful.
Being very slow and deliberate in the training process and not rushing training is important when you have someone who has English as a second language and if the trainer only speaks English. A trainer in this situation should be creative and take adequate time to provide the training in a way that helps a person learn better and includes developing foundational understanding about what are the key takeaways the cleaners should learn. Subsequently the trainer should check their understanding before completion and then again later just to make sure the language wasn’t an insurmountable barrier.
Some creative approaches to language differences are the use of videos to show and explain concepts and tasks. Sometimes the cleaners can review them on their own.
For documentation training, a good start is the introduction to appropriate words to use to describe a situation. An example might be: identify the location, explain in simple terms what was observed and if any action was performed prior to leaving the location. The objective is mainly to assist the individual with direction on how to describe a situation and document it accordingly. Explain to them the importance of clearly communicating to others in writing, as best as they can.
The Contract Model
Contract operating models are very common currently in the pharmaceutical industry, especially for functions like cleanroom cleaning.
For the contract model, there should be a policy or procedure for getting the cleanroom cleaners the specific application tools that they need, and clearly identify who owns the budget. This is important because while the cleaners are not client employees, they should be given the appropriate and adequate tools to use and have the personal protective equipment and training to ensure safe working conditions.
The necessary strong balanced relationship between the employees of a contract firm (cleaners and supervisor) and the management of their contract client firm must be trustworthy, successful and people oriented. Remember, patients are the final recipients of this activity.
Supervision
Managing a cleanroom cleaning team depends on a strong leader and people developer, which is important because they have to work with a diversity of people.
Supervising full-time employees (FTEs) compared with a contract cleaning staff is quite different. For one, contract cleaning staff are likely working second or third shift, while the manufacturing operation staff and supervision may not be. This means that a manager responsible for the cleaning program needs to be willing to flex both hours and communication style in order to stay current with the cleaning staff. When it comes to a day-shift staff, the same shift supervisor can easily speak to or send the cleaning staff an instant message to communicate, but for 2nd or 3rd shift staff, it’s not so simple. In order to be inclusive, and to keep them current with the rest of the team and department news, it is necessary to put in a little extra effort, perhaps by creating online training packages, arranging quick huddles during their working hours, daily or weekly email updates, and videos so that they always have the same information as the manufacturing employees. Another difference is that the manufacturing supervisor overseeing the cleaning program may not be the cleaning team’s only management. As contractors, they’ll have their own company’s management overseeing their work, so it’s important to establish a healthy working relationship with their management. Arrange regular meetings with the contract cleaners’ management in order to provide feedback on the employees, refresh expectations, and troubleshoot any issues. Also, consider inviting them to any client meetings that are held directly with the cleaning staff. This will reduce miscommunication and will ensure everyone is on the same page.
Initial and ongoing communications is important to develop a relationship between a manufacturing operation staff supervisor and a contract staff cleaning team. A manufacturing supervisor should invest some time getting to know their contract GMP cleaning team. Holding weekly or monthly meetings with them provides a way to learn their personalities and preferred communication styles. Keep in mind again that they may be working different hours from operations and the rest of the full-time staff, so be creative with how to communicate. Once you know your team, tailor communications to them. If they’re more visual learners, perhaps consider making PowerPoint presentations or videos for team updates or training. If they like to discuss things in more of a round table setting, arrange quick huddles or check-in calls so that they have the opportunity to ask questions.
The field of parenteral manufacturing is always advancing, and this of course applies to ‘GMP cleaning’ as well. As equipment, technologies, and regulatory expectations evolve, so should be the approach to disinfection. Making it a priority for a supervisor and/or cleaning team members to regularly attend scientific conferences and vendor exhibitions is a helpful approach to keeping current, so that one can continuously explore developments in the cleaning space. Bring in vendors to give new product demonstrations, and always ensure the GMP cleaning staff are included. The cleaning staff are accountable for the cleaning and disinfection application; thus, they need to be included in any conversations regarding new processes, tools, or materials. It’s in a supervisor’s best interest to incorporate their feedback and ideas up front. Not only will this ensure a fit for purpose program that is designed right- first-time, but it will also ensure their active participation, ownership, and buy-in!
Building confidence and pride is an essential component of a contract cleaning team. Without first having a robust GMP cleaning program, all other sterility assurance behaviors and approaches are rendered less effective. In addition to basic GMP and facility disinfection training, a supervisor should talk regularly with the GMP cleaning staff about the relevant products and patients (i.e., what the products are indicated for, what living with that disease is like, etc.), mentioned in this article earlier about role ownership objectives. Making the work personal and meaningful increases their understanding of the important role they play and their commitment to quality. Helping the cleaning team achieve confidence and pride in their role is a fundamental objective of a supervisor.
Summary
The GMP cleaning program is absolutely critical to maintaining the microbiological integrity of a facility, operation, and ultimately the quality of the products. Therefore, the training, oversight, and culture of the GMP cleaning team is just as critical.
Acknowledgments
Many thanks to Madison Hoal and Jane Forbes, Ecolab Life Sciences, for their experienced review of this article.
Note: Contributions to this article by Lauren Sanmartin were written prior to her tenure with Gilead Sciences.
Reference
1. Technical Report No. 90 Contamination Control Strategy Development in Pharmaceutical Manufacturing, Parenteral Drug Association, 2023, Bethesda, MD 2. 2. USP 44-NF39, Disinfectants and Antiseptics, USP Convention
Subscribe to our e-Newsletters
Stay up to date with the latest news, articles, and events. Plus, get special
offers from American Pharmaceutical Review delivered to your inbox!
Sign up now!